MARK OF QUALITY FIRMLY ETCHED
31st July 2012
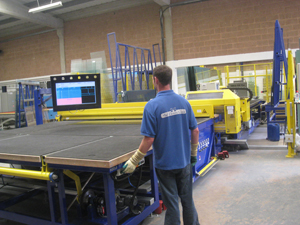 |
Product diversification and the long-term efficiency of Mid Devon Glass were the primary focus for senior management when making a recent investment in Hegla laser technology.
Having initially installed a cutting and loading system the company introduced a laminated solution as part of the existing installation to increase its product portfolio which caused a growth in production
The choice to retrofit Hegla laser technology was brought about because of the positive impact Hegla cutting automation had created in production. For Mid Devon Glass the purchase was considered a ‘lifetime investment’ as the reliability of the equipment could not be matched.
MD Kevin Squibb took the long-term approach when evaluating the company’s needs by considering the efficiency of the entire production line, the increased output and the future direction of the market.
The laser brings substantial time saving benefits in a number of ways including internal efficiency as nothing can be lost. Should any errors occur within batches then these can easily be traced and pinpointed which quickly speeds up the source of any problem.
Kevin comments, “The time saving benefits of the laser will be unique to every business and how it is batched. No-one will be able to fully grasp the advantages until it has been installed as every production line has different requirements. The bigger the output however, the easier it is to see the positive benefits.”
Once having invested in Hegla cutting technology it forced the company to evaluate production methods and the future market. From this point onwards it became evident that in order to become as efficient as possible that the laser marking system was a crucial investment that would stand the test of time.
Technical benefits of the laser will now simplify more complicated procedures such as triple glazing, which will become an increasingly important element to production. As a fully automated system the laser will ensure that a lot of potential problems which can occur manually during the marking process are eliminated. This ultimately will make the entire factory more efficient whichever way you look at it mistakes cost money.
The laser system gives the glass a unique number generated from the company’s production software which is easily identified as it moves down the production line and which ultimately improves the flow and and enhances customer services.
Kevin continues: “The secret of success is self sufficiency. As an established manufacturer of sealed units the commercial and domestic market recognises the capability and reliability of this company. As a family business we had worked hard to maintain a strong corporate position.
Four years ago we experienced fundamental growth which enabled us to triple the size of the production facility. This enabled us to spread the processing types and we introduced toughened glass into the portfolio. Our investment in Hegla has all been geared towards improving services for customers with a broader product range and more efficient deliveries.”
Essentially the Mid Devon Glass laser installation now ensures fewer production downtime and the ability to grow as new industry standards and changes are introduced. The Clear Thinking Software program has been amalgamated into the system enabling a broad range of options to be produced on the glass including shapes, logos, etching orientation and batch numbering.
Kevin concludes: “For us, the Hegla equipment offers major advantages over other equipment on the market. Whilst the technical benefits were paramount for this business we also required that the efficiency, as a long term investment, would reduce costs on a daily basis for a long time.”
|