Interpretation of Part K ‘increasing cost and risk’
8th January 2019
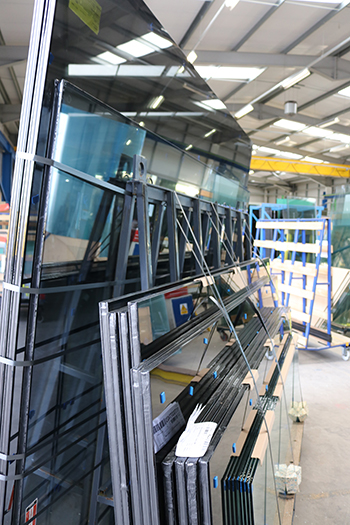 |
The ‘interpretative’ nature of specification under Part K has come under scrutiny from one major processor, saying the spec for protection from falling, collision and impact, can be interpreted ‘wildly differently’ by individual building control officers.
Cornwall Glass says this means that in many cases product is being over-specified, artificially inflating costs, but more worryingly, it also means that some specifications are falling considerably short of loading and containment requirements, representing a risk of injury and death.
Estimating and Technical Representative Ceawlin Hickman said: “Part K, in common with some other areas of building regulations, sets out the requirement for loadings in specific IGU and balustrading applications but isn’t explicit as to how they’re to be achieved. This means it’s down to interpretation of requirement, which in our experience can be wildly different from one control authority to the next. It also means that installers, builders and structural engineers are frequently defaulting to a catch-all specification, which can artificially inflate their costs compared to those of their competitors.
“Much worse, they’re not getting it right and putting lives at risk.”
He highlighted a recent industry horror story where a Juliette balcony without a head rail was signed off by a building inspector having used only a single sheet of 10mm toughened glass, adding: “As a minimum it needs to be a 21.5mm toughened laminate.
“There are significant differences in requirement if it’s a u-channel or post and rail system and the industry and building inspectors are not necessarily always tuned into them.”
This he warned was another key challenge in specification of large IGUs, including applications in floor to ceiling installations with requirements for containment as specified in Part K frequently overlooked.
This sets out the requirement for provisions for containment in all doors and windows where there is a change in floor surface height of 600mm or more in residential applications and 380mm in commercial ones.
“We talk to some people who are very switched on and know exactly what they need because they’re specialists. Where we’re seeing increased risk is that growth in the popularity and architectural application of glass means floor-to-ceiling glass installations are increasing.
“Installation of a 2000mm x 2000mm or 4m2 plus IGU requires much more consideration than simply handling. You need the right specification of glass, something which introduces greater challenge, the bigger you go.
“We’ve seen growth because we work with our customers to get specifications right. Sometime that’s meant working with them to take building control through specifications of IGUs or balustrading to explain how products meet Part K.
“That doesn’t by default mean always moving to a laminate, something which can deliver significant savings on larger contracts.”
www.cornwallglass.co.uk
|